- Bleeder Resistor
- Function of bleeder resistor
- Bleed resistor for start capacitor
- Bleed resistor on run capacitor
- Bleeder resistor circuit
- SSR bleeder resistor
- How to test a start capacitor with a bleed resistor?
- How to calculate Bleeder resistor value?
- What is a bleed down resistor?
- How do I choose a bleeder resistor?
- Function of bleeder resistor in dc power supply
- Frequently asked questions
What is bleed resistor ?
Bleeder Resistor:
This is a standard high-value resistor (connected in parallel with the filter capacitor) used to discharge the capacitor in a filter circuit and primary purpose of using a bleeder resistor in any circuit is safety.
The discharging of the capacitor is very important because even if we turn off the power supply, the charged capacitor can give an electric shock. So it is essential to add a bleed resistor to avoid any mishap.
The function of bleeder resistor:
Let us assume a rectifier with a capacitor filter connected to a power supply. Now, there can be no load present in the circuit, whenever the diode is forward-biased, the capacitor gets charged. As a result, the capacitor produces some voltage across it.
When the diode is reverse biased, the capacitor discharged by a resistor. If the load resistor is not connected, the voltage will be there across the terminals. Now, if we turn off the AC supply, the capacitor still holds some charge. So, if someone touches the terminals, he may get an electric shock. If we can create a discharge path for the capacitor, then We can solve this problem.
Therefore, we connect a highly valued resistor in parallel with the capacitor. This resistor provides a discharge channel for the capacitor. Therefore, it is known as a bleeder resistor.
Bleeder resistor in filter circuit:
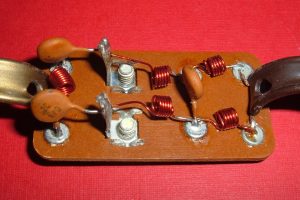
As we have seen, filter circuits make use of bleeder resistors to ensure safety. Let us think of a simple circuit where a capacitor is attached to the main circuitry. Now once the power supply is ON, the capacitor gets charged. After some time, it reaches the peak value and then starts discharging.
The capacitor remain charged for some seconds after the power supply is OFF. If the capacitor is of very high value, severe problems can happen. First, the capacitor may give a substantial electric shock. Second, if a resistor is connected in parallel, the capacitor gets discharged through this resistor.
How to test a start capacitor with a bleed resistor?

Bleed resistor for start capacitor
A capacitor is an energy-storing device. Engineers use this to perform various operations in an electric circuit. First, the capacitor is tested to determine if it is working correctly or not.
When a capacitor is placed in a circuit where the current is flowing, an electric charge builds up on the capacitor plates and after some time, the capacitor accepts no charge, and it means that the capacitor is totally charged. If the circuit requires a charge, the capacitor discharges until the entire charge returns to the circuit.
Following are the steps for testing a start capacitor with a bleed resistor:
- We short the capacitor terminals using a metal contact.
- Digital multimeter readings are taken.
- The power supply is turned on, and we measure how much time the capacitor takes to charge 63.2% of the supply voltage.
- We calculate the time constant of the capacitor and further determine the capacitance value.
If the voltage rating is the identical or more than the older one, we can say that the start capacitor is working fine.
The bleed resistor on run capacitor:
A run capacitor is a device that optimizes a motor’s performance by adjusting the current and the phase shift. The main difference between a run capacitor and a start capacitor is the first one works continuously, and the second one works in cycles like a switch. As there’s no need for the switch in a run capacitor, the bleed resistor is also unnecessary.
Bleeder resistor design:
A bleeder resistor works when the load resistor is disconnected.
A bleed resistor functions best when it is situated at the 1st capacitor after rectifier, doesn’t draw much current, but it can still cause a volt-drops if connected in series. That’s why the components are connected in parallel.
Bleeder resistor circuit:
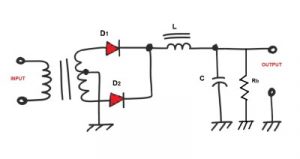
The above rectifier circuit initially consists of an AC power supply, a heavy-duty transformer, two diodes D1 and D2, filter choke L, and filter capacitor C. This capacitor is a large electrolytic capacitor. Therefore, the voltage charging up the capacitor would be very high. However, when we switch the power supply down, a significant voltage still stays for quite some time. So a resistor Rb is connected, which helps in discharging the capacitor.
How to calculate Bleeder resistor value ?
Bleed resistor formula
The mathematical formula to find bleeder resistance requirement is
Rb = – t/C x ln Vt/Vi
Where C is the capacitance value.
- t is the time needed for the capacitor to discharge via the bleed resistor.
- Vt is the voltage up to which the capacitor can be discharged
- Vi is the initial voltage on the capacitor
- We cannot exactly specify the value of Vt. However, any low value of Vt serves the purpose.
Treble bleed resistor value
Treble bleed circuits are typically used in guitars. These are standard high-pass circuits that consist of a capacitor soldered to the center and the outside lugs of the volume control. When resistors are used in the treble bleed circuit, they attenuate the high frequencies so that the signal frequency remains balanced. Though there’s no specific information available about the resistor value, it ranges from 120 Kohm to 150 Kohm.
Treble bleed without the resistor
Treble bleed mods are used in some guitars. A resistor might be wired in parallel with a treble bleed or might not be used at all. They can have slightly different effects on the control. However, the tones appear to be the same with or with out the resistor.
Start capacitor bleed down resistor
The bleed-down resistor is the resistor used with the start capacitor. Here “bleed” means to pass. The bleed-down resistor is used to pass off the residual voltage in the start capacitor after removing it from the motor circuit. Though a bleed-down resistor is a safe way, there are other ways to reduce the residual voltage. The resistance value should be somewhere between 10k ohms to 20k Ohms and resistors are generally crimped to the terminals of the start capacitor.
led bleed resistor:
One of the most challenging jobs in LEDs is to improve the dimming of LED lamps in TRIAC dimmers. As these do not have a resistive load, TRIACs intermittently turn off and on and create the flickering effect. This effect degrades the dimming.
To cope up with this issue, LED designers are now introducing bleeding circuits. A small bleed resistor, when used with a capacitor, is called the bleeding circuit. In the LEDs, the bleed resistor is only turned on when needed. Therefore, a trade-off is established, power consumption is lowered, and greater efficiency is attained.
Static bleed resistor:
The bleed resistors are used in Kite antennas for a static build-up. It reduces the voltage observed across the front end of the radio.
Function of bleeder resistor in dc power supply
There are three primary functions of a bleeder resistor.
- The primary function of a bleed resistor is to provide safety. The capacitor of the filter starts charging when we connect the main supply with the circuit. The capacitor reaches its peak and gradually discharges. Even when the discharging process ends, some excess charge remains in the circuit, and it can give an electric shock to anybody touching the circuit. A bleed resistor connects in parallel help to pass the extra charge thru it.
- The bleed resistor may act as a voltage divider too. If the equipment is supposed to generate 2 or multiple volt-supplies, the device can be tapped, and the bleed resistor can act as a substitute for the series circuit.
- Another important use of the bleed resistor is voltage regulation. Mathematically, voltage regulation is the ratio of the diff in between full load and no-load voltage with the full load voltage. As the difference increases, the voltage regulation improves. To attain this, we need to join the bleed resistor in parallel to the filter circuitry and the load resistor, volt-drop occurs in the bleed resistor, this can acts as a voltage regulator too.
SSR bleeder resistor:
SSR refers to the solid-state relays. A solid-state relay is a four-layer switching device that turns OFF and ON if any external voltage is applied across the control terminals.
The leakage current of the SSR circuit on the input side may cause a reset failure. Insertion of a bleed resistor can help prevent this.
The bleeder resistance value must be set so that the SSR input voltage is a maximum of 0.5 V. when the Relay is OFF.
Reset failure may occur due to solidstate relay leakage current and If this current is higher than the load release current, the solidstate relays may face resetting failure and to increase the Solid-state relay switching current, this resister are adjoined in parallel.
Bleeder resistor tube amp.
The bleeder resistor is not a typical electronic device that is used in everyday gadgets. However, some special equipment like musical instruments, amplifiers contain bleeder circuits. The tube amplifier is such a device. The bleed resistor connected in parallel with the amplifier circuitry easily discharges high voltage capacitors.
ESD bleeder resistor
ESD stands for electrostatic discharge. This discharge might cause damage if not done correctly. So the testing of ESD must be done even it is time-consuming one. Here, the device requires 470 Kohm resistors connected to the ground. The presence of a bleed resistor drastically changes the test results. But the bleeder resistor is needed so that during testing, nobody gets an electric shock.
The most common value for a bleeder resistor
The ratings of the bleeder resistor varies in every circuitry. For example, for a start capacitor AC motor, the value ranges from 10k ohm to 20k ohm. For some other filter circuits, the value can even be more than 200k ohm.
FAQs
What is the bleeder resistor used for?
A bleeder resistor is majorly used in filter circuits to add to the safety and prevent electric shock.
How do I choose a bleeder resistor?
There is always a trade-off between the speed of the bleeder and the total power waste and low values of bleed resistors give a faster time for discharging, but they will give more power loss. We may choose the value with the help of this equation:
Vt = Vie-t/RbC
Where Vt is the instantaneous voltage across the capacitor
Rb is the bleeder resistance
Vi is the initial voltage
t is the instantaneous time period, and C is the capacitance value.
What is a bleed down resistor?
A bleed down resistor is seen in a motor circuit where there’s a built-in start capacitor. The capacitor usually operates for very short instances while the motor is coming up to speed, if the motor speed up, the capacitor is not required after speeded up. So there should be a switch or voltage sensing device to pull the capacitor out of the circuit. But even after the capacitor is pulled out, for a few seconds, the voltage remains high. It may cause hazards. Therefore a resistor is connected to bleed down the voltage. It is known as a bleed down resistor.
What is bleeder resistance?
This is the resistive value of the bleed resistor in ohm.
How do I select the value of the bleeder resistor to discharge a capacitor at the DC bus automotive inverter application?
The bleeder resistor value should be very high if we want to lower the power consumption when the inverter is kept on. Similarly, the value should be such that the capacitor gets discharged fast.
Why does a DC/DC converter have a bleeder resistor at its output?
The DC/DC converters regulate substantial output capacitance and low load. So, after the device is turned off, there can be a considerable amount of charge left. This charge may take up to several minutes to be discharged and may give a shock to anybody working with it. Therefore, a resistor is attached to the output to fasten this discharging process.
Why do some capacitors have resistors attached to them?
Sometimes capacitors with high value contain resistors so that the stored charge gets drained fast after the power supply is turned off. This resistor provides a discharge channel for the capacitor. Therefore, it is known as a bleeder resistor.
How to use a discharge resistor?
The discharge resistor must be kept in parallel with the circuit so that it can drain the excess charge.
The discharging of the capacitor is very important because even if we turn off the power supply, the charged capacitor can give an electric shock. So it is essential to add a bleed resistor to avoid any mishap.
How do an X rated capacitor and a bleed resistor reduce the voltage in a transformerless power supply?
X rated capacitors have high voltage ratings that can directly be used with AC mains in series. Here the capacitor is used as a voltage divider. Along with the capacitor, the circuit contains a Zener diode and a rectifier with the bleed resistor. The capacitive reactance helps in reducing the voltage.
Why do you need a bleed resistor on the start capacitor?
The start capacitors make use of a bleed resistor to accomplish any task safely after the power supply is turned off.
The function of the bleeder resistor is-
- To keep the circuit safe from hazards
- To draw high current
- To optimize the efficiency of the rectifier
- All of the above
Answer: The bleed resistor provides a channel for the capacitor to discharge the remaining charge. Thus it saves the circuit from undesirable accidents.
Which of the following statement(s) is/are true about the bleeder resistors-
- The bleeder resistors are connected in parallel with the main circuit
- A bleeder resistor prevents the amplifiers from being over-driven
- The bleeder resistors can act as voltage regulators
- None of the above
Answer: 1 and 3 are correct option. The bleeder resistors are connected in parallel so that they can quickly discharge the capacitor. These can also work as voltage regulators by creating differences between load voltages.
The function of a bleeder resistor in a power supply is
a. To amplify the voltage
b. Discharge the stored charge on the capacitor
c. To increase the output current
d. All of these
Answer: The bleed resistor is used to discharge the capacitor as soon as possible so that no one gets an electric shock while touching the circuit and nothing to do with the current.
How to Calculate bleeder resistor power supply ?
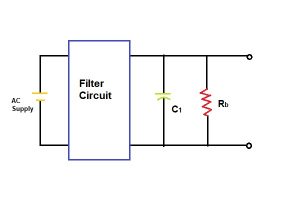
Let us take a filter circuit connected to an AC supply voltage and has a capacitor with a capacitance value of 2 micro Farad. The initial voltage Vi is 1000 volt, and Vt is 10 volt. The discharging time is 5 seconds, then using the formula, we can calculate the value of the bleed resistor needed to discharge the capacitor.
We know, Rb = -t/[C x ln(Vt/Vi)]
Therefore, Rb = -5/[2 x 10-6 x ln(10/1000)] = 542,888 ohm