- When force transmits from one body to another, forces parallel to the surface are experienced by the body, such kind of forces produce shear stress.
- It is vital to know about the shear stresses acting on the material while designing the product. Shear failure is the most common failure which occurs due to inappropriate consideration of shear forces.
Shear Stress Definition
- When the applied force is parallel/tangential to the surface area of application, then the stress produced is known as shear stress.
- Here application of force is tangential to the surface of application.
- A component of the stress tensor in the direction parallel to the area of application.
- Shear stress also occurs in axial loading, bending, etc.
Shear Stress Formula
Shear Stress= Force imposed parallel to the area/ Area of cross-section

What is Shear Stress Units ?
Unit of shear stress is N/m2 or Pa.
In industries, the unit used to measure shear stress is N/mm2 or MPa (Mega Pascal)
Shear Stress Symbol | Shear Stress tau
The symbol used to represent shear stress is τ (Tau). It is also represented by T.
Shear Stress Diagram

Shear Stress Notation
- Symbol τ is used to represent shear stress.
- To show the applied force and direction of the application area, subscripts are used with the symbol τ as τij.
- Where i represent the direction of the surface plane on which it is being applied (perpendicular to the surface), and j represents the applied force’s direction.
- Thus, τij= Shear stress acting on the i-surface in j-direction.
τji= Shear stress acting on the j-surface in i-direction.
- We can write it as:

Shear Stress Direction
In 2 Dimensions:

- In the vector form, shear stress is the ratio of a parallel component of force applied to the unit normal vector of area.
τ= F‖ / A
In 3 Dimensions:
- In naming xy, which is in the subscript form (subscript convention), index x represents the direction of a vector perpendicular to the application area, and y represents the direction of applied force.
- In the following figure, it is represented for all three axes.

Any of the shear stress can be represented as follow:

Shear Stress Sign Convention
When the shear stress is applied on a surface along the principal axis, the adjacent perpendicular axis experiences the equal amount of shear stress in the opposite direction known as complementary shear stress as shown in the figure:

- Shear stress is positive if the shear force applied along the x-axis is in the right direction or clockwise.
Similarly, Shear stress is positive if the shear force applied along the y-axis is in an upward direction or it is counterclockwise.
- Shear stress is negative if the shear force applied along the x-axis is in the left direction or in counterclockwise.
Similarly, Shear stress is negative if the shear force applied along the y-axis is in a downward direction or it is clockwise.
- Half arrowheads are used to represent shear stress.

Shear Strain
- When the shear stress is applied on a surface, deformation is produced in the material. So, the ratio of deformation to the original length perpendicular to the member’s axes is known as shear strain. It is denoted by γ.
- It is also defined as the tangent of the strain angle ө.
- Shear Strain= del l/ h = tangent(Ө)


Shear Stress and Shear Strain
- It is noted that shear strain is dependent on shear stress. The relation is expressed as

Modulus of Rigidity | Shear Stress Modulus | Shear Modulus of Rigidity
- The proportionality constant G is known as Modulus of Rigidity or Shear Stress Modulus or Shear Modulus of Rigidity.
- Thus,
Modulus of Rigidity = Shear Stress/ Shear Strain

- In most of the metals, G is about 0.4 times of Young’s Modulus of Elasticity.
For isotropic materials, Modulus of Rigidity and Modulus of Elasticity is related to each other according to
Y = 2*G* (1+ ʋ)
Where, Y= Modulus of Elasticity
G= Modulus of Rigidity
Shear Strength
- Shear strength is the maximum value of shear stress that can resist failure due to shear stress.
- It is a significant parameter while designing and manufacturing machines.
- Example: While designing bolts and rivets, it is indispensable to know about the material’s shear strength.
Shear Stress vs Normal Stress
Shear Stress | Normal Stress | |
1. | Force applied is parallel to the surface on which it is being applied | Force applied is perpendicular to the surface on which it is being applied. |
2. | Force vector and area vector are perpendicular to each other | Force vector and area vector are parallel to each other. |
Shear Stress from Torque | Shear Stress Due to Torsion
- Torque is a rotational form of force which makes the object to rotate around an axis. When this torque is applied on a deformable body, it generates shear stress in that body, making that body twist around an axis, known as torsion.
- This type of stress is significant in shafts. The stresses or deformations induced in the shaft due to this torsion are shear kinds of stresses.
- The shear strain produced in the following shaft of radius r is represented as follows:
γ= rdө/dz

Thus, the shear stress produced is represented by

Shear Stress Fluid
- Shear stress produced in any material is due to relative movement of planes on each other.
- When it comes to fluid, shear stress is produced in the fluids due to relative movement of fluid layers on one another. It is the viscosity which causes shear stress in the fluid.
- Due to shear stress, fluid cannot be held in one place.
- Thus, the shear stress produced in the fluid is equal to the

Where μ= Dynamic Viscosity
u= Flow Velocity
y= Height above the boundary
- This equation is also known as Newton’s Law of Viscosity.
Read more about Shear Strain and All important facts
Shear Rate
- Shear rate is the rate at which one layer of fluid passes on another adjacent layer of fluid; this can find out by both using geometry and speed of the flow.
- The viscosity of fluid mainly depends upon the shear rate of the fluid.
- This parameter is very important while designing fluid products like syrups, sunscreen cream, body lotion, etc.
Shear Stress vs Shear Rate
- The shear rate is defined as the rate of change of velocity of layers of fluid on one another. For all Newtonian fluids, the viscosity remains constant when there is a change in shear rate, and the shear stress is directly proportional to the shear rate.
- Following is a graphical representation of shear stress vs shear for a different type of fluid:
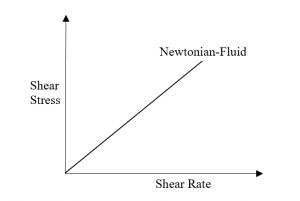
Shear Stress in Beams
- If a cantilever beam of diameter d is twisted on its free end, if torsion of magnitude T is applied on its free end, then the shear stress produced in the beam.
- This shear stress is represented as follows


Shear Stress due to Bending
- For an ideal case, shear stress does not produce due to bending, but in real condition, shear stress occurs in the bending conditions.
- A varying bending moment along the length of the beam causes movement of one plane on another because shear stress gets produced in the beams.
Read more about Shear modulus and Modulus of rigidity
Shear Stress in Bolts
- Bolts are mainly used to fix two different assembly bodies like joints, two different metal sheets, two different pipes of an assembly etc.
- The bolt experiences shear load or shear force due to the presence of two different loadings acting in the different directions this causes one plane of the bolt to slip on another plane of the bolt.
- ; This causes shear failure in joints like cotter joint, knuckle joint, etc. so, while selecting material for different mechanisms, it is essential to know its shear stress.
- Double shear stress is calculated in bolts.

Shear Stress Steel
- Steel is one of the most applicable metals in all types of industries. From constructions to machines, steel is used everywhere. Therefore the maximum shear stress value of steel is a significant parameter while designing.
- It is determined using the ultimate tensile strength of the steel. Von Misses factor is used to determine maximum shear stress. It states that maximum shear stress is 0.577 times of the ultimate tensile strength.
- In many cases, it is considered as 0.5 times of ultimate tensile strength of the steel.
Read more about How to calculate shear strain
Shear Stress Problems
Subjective Questions
What is Shear Stress?
Ans.: When the applied force is parallel to the surface/area of application, then the stress produced is known as shear stress. Shear stress is a component of the stress tensor in the direction parallel to the area of application.
What is complementary shear stress?
Ans.: When the shear stress is applied on a surface along the principal axis the adjacent perpendicular axis experiences the equal amount of shear stress in the opposite direction known as complementary shear stress
What are the sign conventions for shear stress? | How to decide sign of shear stress?
Ans.: Shear stress is positive if the shear force applied along the x-axis is in the right direction or clockwise.
Similarly, Shear stress is positive if the shear force applied along the y-axis is in an upward direction or it is counterclockwise.
Shear stress is negative if the shear force applied along the x-axis is in the left direction or in counterclockwise.
Similarly, Shear stress is negative if the shear force applied along the y-axis is in a downward direction or it is clockwise.
What is the sign for shear stress?
Symbol τ is used to represent shear stress. To specify the directions of applied force and direction of the application area, subscripts are used with the symbol τ as τij.
What are examples of shear?
When a piece of paper is cut with the scissor.
A bolt and nut tightly fixed with plates.
Rubbing palm on each other
Any friction leads to the production of shear.
What’s an example of shear stress?
Painting walls using colour.
Chewing food under the teeth.
In cotter and knuckle joints, cotter and knuckle experiences shear stress.
How do you solve shear stress?
Shear Stress= Force imposed parallel to the area/ Area of cross Section

What causes shear stress?
When force transmits from one body to another, forces parallel to the surface are experienced by the body, such kind of forces produce shear stress.
What is the difference between shear stress and shear force?
Shear force is the force applied parallel or tangential to the plane’s surface, whereas shear stress is the shear force experienced by the plane’s surface per unit area.
What is the difference between shear stress and shear rate?
When the applied force is parallel to the surface area of application, then the stress produced is known as shear stress whereas the shear rate is the rate at which one layer of fluid passes on another adjacent layer of fluid.
What is a positive shear force?
Shear stress is positive if the shear force applied along the x-axis is in the right direction or clockwise. Similarly, Shear stress is positive if the shear force applied along the y-axis is in an upward direction or it is counterclockwise.
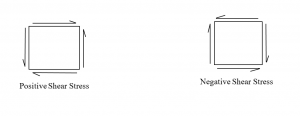
What is average shear stress?
Actual shear stress is never uniform; it is different for the different unit cross-sectional area. So, to calculate this shear stress, the considered shear stress is the average shear stress.
Average shear stress is always lesser than maximum shear stress for the given area of cross-section.
What is Shear Strain?
When the shear stress is applied on a surface, deformation is produced in the material. So, the ratio of deformation to the original length perpendicular to the member’s axes is known as shear strain. It is denoted by γ.


Is shear strain in radian?
No. shear strain is the tangent value of del l and h, which is a unitless quantity.
Objective Questions:
A block of a material with a shear modulus of rigidity G = 90 KPa is bonded to two rigid horizontal plates. The lower plate is fixed, while the upper plate is subjected to a horizontal force P. knowing that the upper plate moves through 0.04 cm under the force’s action if the height of the block is 2cm, determine the average shearing strain in the material.
- 0.04 rad
- 0.02 rad
- 0.01 rad
- 0.08 rad
Solution: Option 2. Is the answer.

A block of a material with a shear modulus of rigidity G = 90 KPa is bonded to two rigid horizontal plates. The lower plate is fixed, while the upper plate is subjected to a horizontal force P. knowing that the upper plate moves through 0.04 cm under the force’s action if the height of the block is 2cm, find the force P exerted on the upper plate.
- 180
- 360
- 720
- 90
Solution: Option 1. is the answer.


Find the value of shear stresses developed in the pin A for the bell crank mechanism shown in the figure? Find the safe diameter of the pin if the allowable shear stresses for the pin material is180 MPa.
- 3mm
- 4mm
- 4.5mm
- 5mm
Solution: Answer is option 4.
Stresses developed in pin are shear stress and bearing stress.
Force at B= 5*0.1/0.15= 3.33KN

Considering double shear at A

The safe diameter of pin is more significant than 4.6mm.
Which of the following basic assumption is not considered while deriving torsion equation for a circular member?
- The material must be homogenous and isotropic.
- A plane perpendicular to the axis remains plane also after the torque application.
- Shear strain varies linearly from the central axis in a circular member when subjected to a torque.
- The material does not obey Hooke’s law
Solution: Option 4.