In the article briefly we are going to discuss the topic about the “Milling machine working.” . Milling machine working principle is needed to operating the machine tools.
To get the right features of the material is following the steps:
In milling machine process the metal is removed by followed the steps to creating different types of features to cutting the excess unwanted materials.
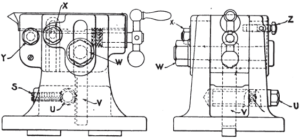
Image credit – Wikimedia Common
How a milling machine tool is working on a tool is briefly discusses in below section,
Time of loading or unloading:
For the installation of the workpiece which is attached to the milling machine tool and then whole setup is again fixed with the fixture and in the final of the process the final product need to unload. The time of loading or unloading is depended on some parameters. The parameters are size of the workpiece and fixture, complexity and weight of the fixture and workpiece.
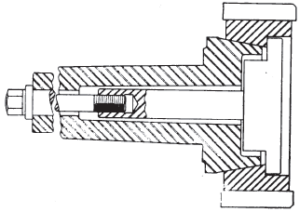
Image Credit – Wikimedia Commons
Cutting time:
From the term of the workpiece we could easily understand that the time required for the edges cutting of the workpiece and the fixtures for each and every operations of the milling machine tool. The cutting time can be explain as the required time which is calculated the whole amount of the length which is divided by the feed rate for the particular milling operations that is the speed to the relative cutter of the workpiece or fixture.
Idle time:
The term of idle time means the time which is not productive. The idle time can be explain as the time period of the milling machine operation process which is not engaging the cycle of the process to the fixture and unwanted excess amount of material is removed and get desired shape and size of the material’s part.
The idle time of the process is also included adjusting the setting of the machine, movements of the tools into the features, changes of the machine tools and also approaching the work tool and after that workpiece is reacting.
Read more about The correct way and solved problems and Facts
Time of the tool replacement:
At the last of the process the steps is happed that is the tool replacement. A particular time is needed to replace the tool of the milling machine. The time of the tool replacement is exceeding the time period of the tool that is the main reason behind the worn to cut the effectiveness. The time of the tool replacement is not performed each and every time process cycle but it’s only happed when the tool is reaches to its life time period.
For calculating the time period of the tool is replacement with the time and it is adjusting for making the particular single part which is multiplying with the frequency, in this way the cutting time of the tool is divided by the lifetime of the work tool.
The milling machine mainly a process of material removes. In any field of production engineering industry there a lots of machine and machine tools are used to do a wide range of operation in the work piece among them milling machine is. By the help of this machine tool a wide range of cutting can so easily without facing any difficulties in the work piece or fixtures.
Milling machine such as operation by which we can easily work with asymmetric material. The asymmetric materials contain a lot of features that can be pockets, internal threads, making surface of the material flat, external threads, revolutions making of the surfaces of workpiece, 3D surface counters, holes or sockets. It works against the fed which is a rotating cutter with multipoint. The multipoint cutter is rotates in a higher speed at the speed of removing the workpiece material is too high.
Required a certain time period to achieving the fixed features of the workpiece with in a cycle time included the setup of the initial time period for each and every steps of the milling machine tool.
Milling machine types:
The milling machine tool is one of the most useful machines among the all machine tools used in the production industries. It is the main operation of machining process. The process is working to feed the fixture besides using a turning tool. Several edges with cutter is contains by the turning cylindrical tool.
In a production industry by the capacity of metal removing rate mainly five types of milling machine is classified. The classifications named are,
- Knee and column type milling machine tool
- Planer milling machine tool
- Fixed bed type milling machine tool
- Centred machining machines tool
- Individual type of milling machine tool
The classified milling machines descriptions are given in below section,
Knee and column type milling machine tool: One of the most common and oldest milling machines is knee and column type milling machine.
These are one of the most common used milling machine tool in the industry of the production.
This also can be categorized in four parts. They are,
- Vertical milling machine
- Universal milling machine
- Hand milling machine
- Horizontal milling machine
Planer milling machine tool: The planer milling machine is almost same as the fixed bed type milling machine.
Fixed bed type milling machine tool: In this type of milling machine the table is situated directly to the bed of machine tool and attached with head and cutters which help to do the operations into the workpiece.
This type of milling machine tool is also can be categorized in three parts. They are,
- Simplex milling machine tool
- Duplex milling machine tool
- Triplex milling machine tool
Centred machining machines: Now a day the milling machine is worked by the computer. The Computer numerical control machines are gives more accrue and define workpiece. With this versatile machine can be attached and do a lots of type operations like boring, milling, drilling tapering and many more.
Individual type of milling machine tool:
The type of this milling machine tool is given below,
- Duplicating milling machine
- Continuous milling machine
- Planetary milling machine
- Pantograph milling machine
- Drum milling machine
- Profiling milling machine
- Tracer and profiling milling machine
When the motion of milling machine tool is controlled by the electric the classifications names are maintained in below,
- Transfer lines milling machine
- Flexible manufacturing system milling machine
- Flexible manufacturing cell milling machine
- Centerd machining milling machine
- CNC programming milling machine
- Data input manually milling machine
Uses of milling machine:
A milling machine is a process of machining where material is removed with the help of the rotary cutters. The operation of the milling machine can be done in various directions that could be one or more than one axes, pressure and head speed of the cutter. The milling machine operations can be done in various metals that could be large, small, heavy or light. In below we are going to discuss about the application of the milling machine,
- Gears which are in various types and shapes are made by the milling machine.
- In the workpiece slot and grooves are easily made by the milling machine.
- Complicated shapes are also can be make in the workpiece.
- Make flat the surface of workpiece and countered surface is also can make with it
- Slotting is done by this machining process.
Milling machine examples:
The example of milling machine is discuss in below,
Horizontal milling machine: Horizontal milling machine another name is plain milling machine. The horizontal milling machine contains a spindle which is situated in horizontally. The table of this machine can be feed in any direction means it can be feed cross sectional or vertically neither horizontally.
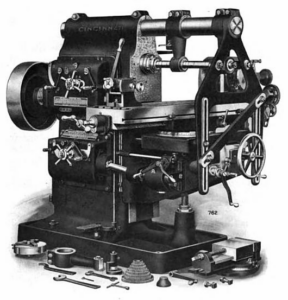
Image Credit – Wikimedia Commons
In the horizontal milling machine the feed can be done in three dimensions and their little description is given below,
Vertical – In this the table is adjusted vertically.
Cross – In this dimension the table can moves parallel to the spindle of the milling machine.
Longitudinal – In this dimension the table of the milling machine rotate.
Read more about Wing Pulley: What Is, Types, Material, Interesting Guide
Vertical milling machine: In the vertical milling machine the present spindle is situated in vertical position to the table of the milling machine. This milling machine is used to do various operations in the workpiece such as grooving, slot and flatten the surface of the workpiece. The head of the spindle is attached with the column vertically which rotate with a motion angularly.

Image Credit – Wikimedia Commons
Universal milling machine: In the universal milling machine a table is attached with the column. The table can rotate in all motions with a dividing head which can changes all the gears that is the reason the milling machine can do any type of operation into the workpiece and we can get a desired part if the material.
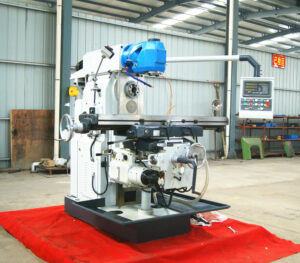
Image Credit – Wikimedia Commons
It included some extra attachments’,
- Rotary attachment
- Index head
- Slotting attachment
- Vertical milling attachment
Planer style milling machine:
Turret milling machine: The turret milling machine is also known as the Bridgeport type milling machine. This is a versatile milling machine tool with the help of it we can proceeds a lot of operation and uses widely in the production engineering.
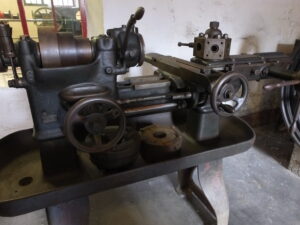
Image Credit – Wikimedia Commons
C Frame milling machine: One of the powerful and sturdy milling machine tool is c frame milling machine. Mainly heavy and large size workpiece are can work on it.
Rotary table milling machine
Column milling machine