To repair an alternator, first test its output voltage (should be 13.5-14.5V). If underperforming, check the drive belt tension and wear. For internal issues, dismantle the alternator; inspect the brushes, rectifier, and rotor for damage. Brushes often need replacing if under 1/4 inch. A multimeter can test the diode rectifier; replace if faulty. Reassemble carefully, ensuring all connections are secure. Regular maintenance can extend lifespan, which averages 7 years or 80,000-150,000 miles.Now lets deep dive into how to repair an alternator.
1. Diagnose the Problem
Understanding Symptoms and Testing
Diagnosing the alternator’s condition is crucial before attempting any repair. This step helps determine whether the alternator is indeed the source of the vehicle’s electrical problems. Accurate diagnosis involves checking for common symptoms such as dimming lights, unusual noises, and a battery that drains quickly.
Voltage Measurement
To accurately measure the alternator’s output, use a reliable digital multimeter. This test checks if the alternator provides sufficient voltage to keep the battery charged and the electrical system functioning. The expected range is critical; anything outside of 13.5-14.5 volts can indicate a failing alternator.
Step | Action | Expected Result | Notes |
---|---|---|---|
1 | Set multimeter to DC voltage | – | High-accuracy multimeters provide more reliable readings |
2 | Connect red lead to battery positive, black to negative | – | Ensure secure connection |
3 | Start engine, idle at 1500 RPM | 13.5-14.5 volts | Readings outside this range suggest alternator issues |
Listening for Unusual Noises
The presence of unusual noises, like grinding or whining from the alternator, often points to mechanical issues, such as bearing failure. Bearings have a limited lifespan and their deterioration can significantly impact alternator performance.
Checking for Overheating Signs
Overheating in an alternator can manifest as a distinct burning smell, indicating possible insulation or wiring damage. This usually occurs when the alternator is overloaded and is forced to produce more current than its design allows.
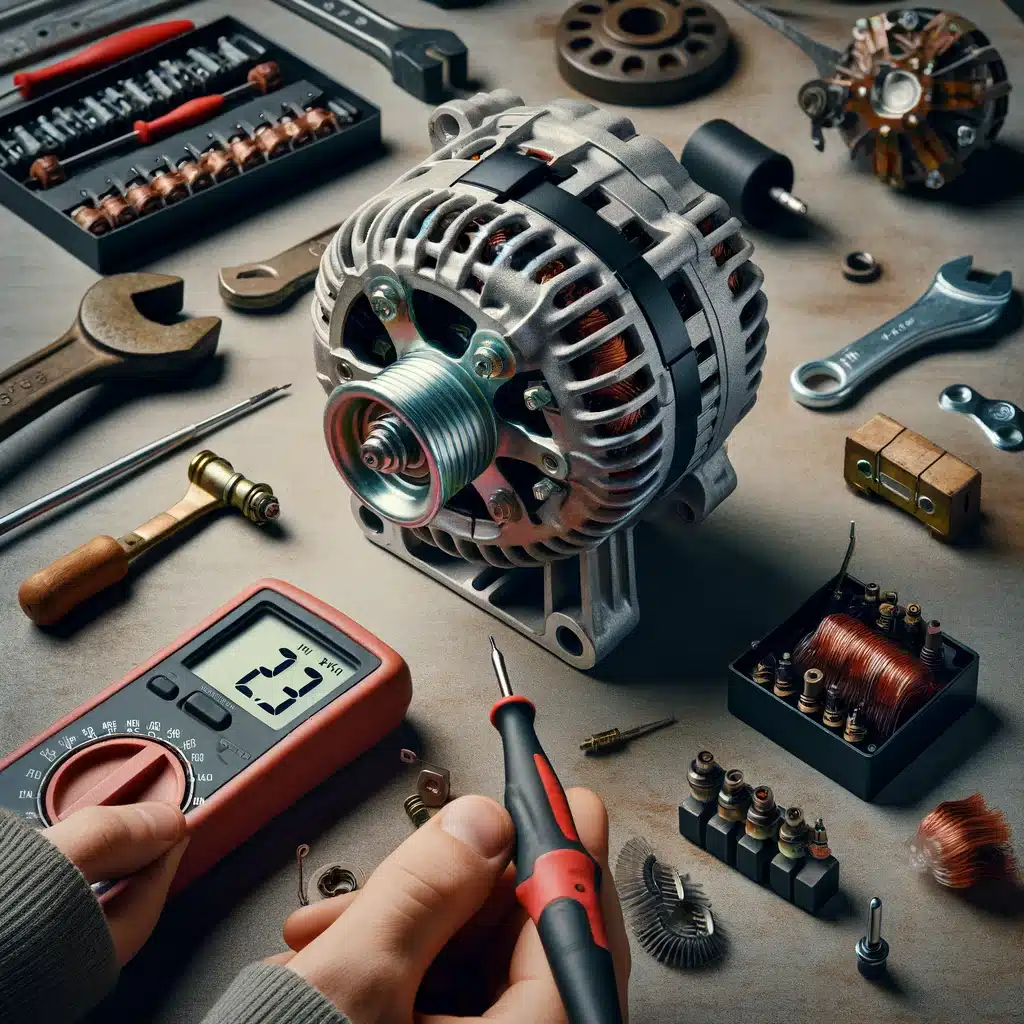
2. Safety First
Precautionary Measures
Working on a vehicle’s electrical system requires strict adherence to safety protocols to prevent accidents or damage to the vehicle. This includes ensuring the vehicle is secure and stationary and that personal protective equipment is worn.
Key Safety Steps
Proper safety measures include parking the vehicle on a level surface, wearing protective gear, and ensuring the ignition is off to avoid accidental engine start. These steps are crucial for a safe and accident-free working environment.
Safety Measure | Description | Reason |
---|---|---|
Level Surface | Park vehicle on flat ground | Prevents movement during repair |
Protective Gear | Wear safety glasses and gloves | Protects against electrical hazards and injuries |
Key Removal | Remove key from ignition | Ensures vehicle remains off during repair |
3. Access the Alternator
Navigating to the Component
The alternator’s location varies depending on the vehicle model. Accessing it might require removing other components, which can be a straightforward or a complex process. This step is critical to reach and inspect the alternator properly.
Alternator Location
Alternators can be top-mounted, making them easily accessible, or located deeper in the engine bay, requiring the removal of more parts. Understanding the specific layout of your vehicle’s engine is essential for efficient access.
Component Removal Specifications
Different vehicles may require various tools and steps to remove components blocking access to the alternator. It’s important to follow the specific guidelines for your vehicle to avoid any accidental damage.
Component | Typical Removal Steps | Tools Required |
---|---|---|
Air Filter Housing | Unscrew clamps, disconnect hoses | Screwdriver, Pliers |
Coolant Reservoir | Unbolt reservoir, disconnect hoses | Socket wrench, Pliers |
4. Remove the Alternator
Detailed Disassembly
Removing the alternator involves several steps, including loosening the serpentine belt, disconnecting electrical connections, and finally unbolting the alternator. Each step must be done with care to avoid damage to the alternator or surrounding components.
Serpentine Belt Removal
The serpentine belt, which drives the alternator, must be carefully loosened and removed. Proper tension is crucial for the belt’s operation; therefore, a belt tension gauge is used to ensure correct adjustment.
Electrical Disconnections
Disconnecting the electrical connections requires attention to detail. Labeling each wire and connector is vital for accurate reassembly, helping prevent potential electrical issues later.
Bolt Removal
Removing the bolts securing the alternator requires attention to their torque specifications. This ensures a secure fit when reassembling and prevents damage from over-tightening.
Bolt Specifications
Proper bolt management is key in alternator removal. Keeping track of the bolt sizes and their respective torque specifications is essential for a successful reassembly process.
5. Inspect and Decide
Detailed Alternator Inspection
After removing the alternator, it’s essential to conduct a thorough inspection to assess its condition. This evaluation is crucial in deciding whether a repair is feasible or if a replacement is necessary. Key areas to focus on include the physical state of the alternator and the condition of its internal components.
Internal Damage Assessment
A detailed examination of the alternator for physical damage, such as cracks or burnt wires, is vital. This inspection can reveal the extent of wear or damage and help determine the practicality of repairing the unit.
Component Wear and Tear
Measuring critical components like the rotor and stator against manufacturer specifications is crucial in assessing the extent of wear. Significant deviations can adversely affect the alternator’s performance and longevity.
Cost-Benefit Analysis
A critical part of the decision-making process is evaluating the costs of repair versus replacement, considering factors like the age of the vehicle and the condition of the alternator. This analysis helps in making an economically sound decision.
Alternator Condition Assessment
This table summarizes the condition of the alternator and the recommended actions, providing a clear guide for decision-making.
Condition | Action | Notes |
---|---|---|
Visible damage | Consider replacement | Repair may not be reliable |
Minor wear | Repair possible components | Cost-effective for newer vehicles |
Major internal damage | Replacement recommended | Repair may not be economical |
6. Repairing the Alternator
Component-Specific Repairs
Repairing an alternator involves meticulous work on its individual components. Each part, from the brushes to the diodes, requires careful handling and precise refurbishment or replacement.
Brushes
The brushes in an alternator play a crucial role in conducting electricity. Checking their length and replacing them if they are excessively worn is important for maintaining the alternator’s efficiency.
Voltage Regulator
The voltage regulator is key in controlling the alternator’s output. Testing its consistency and ensuring it functions within the specified range is essential for the alternator’s effective operation.
Bearings
Bearings facilitate the smooth operation of the alternator. Measuring their dimensions and replacing them if necessary is important to prevent future alternator failures.
Diodes
The diodes are critical for converting AC to DC current. Testing them to ensure they function within the specified range is vital for the alternator’s electrical efficiency.
Detailed Component Repair
This section provides a breakdown of each key component, its specifications, and notes for repair.
Component | Specification | Repair Notes |
---|---|---|
Brushes | >10 mm length | Replace if worn beyond limit |
Voltage Regulator | ±0.5 volts deviation | Replace if outside range |
Bearings | ±0.01 mm tolerance | Replace if out of spec |
Diodes | 0.5-0.7 volts forward bias | Replace rectifier assembly if faulty |
7. Reinstalling
Precise Reassembly
The reinstallation of the alternator is as crucial as its removal. It involves accurately positioning the alternator, correctly tightening the bolts, and ensuring the serpentine belt is properly tensioned.
Correct Positioning and Bolt Tightening
Ensuring the alternator is correctly aligned and secured is essential for its optimal functioning. Using a torque wrench for bolt tightening ensures adherence to OEM specifications.
Belt Reinstallation
Properly adjusting the serpentine belt to the recommended tension is critical. Incorrect tension can lead to belt wear or alternator performance issues.
Reassembly Checklist
This checklist ensures that each reassembly step is accurately completed, guaranteeing the successful reinstallation of the alternator.
Task | Specification | Notes |
---|---|---|
Positioning | Correct alignment | Ensures efficient operation |
Bolt Tightening | OEM torque specs | Prevents over/under-tightening |
Belt Tension | Manufacturer’s spec | Ensures proper operation and longevity |
8. Final Check
Verification of Repair
A comprehensive final check is necessary to ensure the repair’s success. This includes a thorough inspection and testing of the alternator post-reinstallation to confirm everything functions as expected.
Operational Test and Voltage Recheck
Conducting an operational test and rechecking the voltage output are critical final steps. They verify that the alternator repair was successful and that the alternator operates within the required specifications.
Professional Tips
Expert Insights
For successful alternator repair, adhering to specific guidelines and using the right tools are paramount. Referring to the vehicle’s service manual for detailed instructions and using calibrated tools for measurements are essential for a reliable repair.
Expert Advice Table
This table offers quick expert advice on various aspects of alternator repair, emphasizing the importance of precision and informed decision-making.
Tip | Explanation | Benefit |
---|---|---|
Service Manuals | Provides vehicle-specific instructions | Ensures accuracy in repair |
Calibrated Tools | Essential for precise measurements | Increases reliability of repair |
Cost Analysis | Repair vs. replacement | Cost-effective decision-making |
5. Inspect and Decide
Detailed Alternator Inspection
After removing the alternator, it’s essential to conduct a thorough inspection to assess its condition. This evaluation is crucial in deciding whether a repair is feasible or if a replacement is necessary. Key areas to focus on include the physical state of the alternator and the condition of its internal components.
Internal Damage Assessment
A detailed examination of the alternator for physical damage, such as cracks or burnt wires, is vital. This inspection can reveal the extent of wear or damage and help determine the practicality of repairing the unit.
Component Wear and Tear
Measuring critical components like the rotor and stator against manufacturer specifications is crucial in assessing the extent of wear. Significant deviations can adversely affect the alternator’s performance and longevity.
Cost-Benefit Analysis
A critical part of the decision-making process is evaluating the costs of repair versus replacement, considering factors like the age of the vehicle and the condition of the alternator. This analysis helps in making an economically sound decision.
Alternator Condition Assessment
This table summarizes the condition of the alternator and the recommended actions, providing a clear guide for decision-making.
Condition | Action | Notes |
---|---|---|
Visible damage | Consider replacement | Repair may not be reliable |
Minor wear | Repair possible components | Cost-effective for newer vehicles |
Major internal damage | Replacement recommended | Repair may not be economical |
6. Repairing the Alternator
Component-Specific Repairs
Repairing an alternator involves meticulous work on its individual components. Each part, from the brushes to the diodes, requires careful handling and precise refurbishment or replacement.
Brushes
The brushes in an alternator play a crucial role in conducting electricity. Checking their length and replacing them if they are excessively worn is important for maintaining the alternator’s efficiency.
Voltage Regulator
The voltage regulator is key in controlling the alternator’s output. Testing its consistency and ensuring it functions within the specified range is essential for the alternator’s effective operation.
Bearings
Bearings facilitate the smooth operation of the alternator. Measuring their dimensions and replacing them if necessary is important to prevent future alternator failures.
Diodes
The diodes are critical for converting AC to DC current. Testing them to ensure they function within the specified range is vital for the alternator’s electrical efficiency.
Detailed Component Repair
This section provides a breakdown of each key component, its specifications, and notes for repair.
Component | Specification | Repair Notes |
---|---|---|
Brushes | >10 mm length | Replace if worn beyond limit |
Voltage Regulator | ±0.5 volts deviation | Replace if outside range |
Bearings | ±0.01 mm tolerance | Replace if out of spec |
Diodes | 0.5-0.7 volts forward bias | Replace rectifier assembly if faulty |
7. Reinstalling
Precise Reassembly
The reinstallation of the alternator is as crucial as its removal. It involves accurately positioning the alternator, correctly tightening the bolts, and ensuring the serpentine belt is properly tensioned.
Correct Positioning and Bolt Tightening
Ensuring the alternator is correctly aligned and secured is essential for its optimal functioning. Using a torque wrench for bolt tightening ensures adherence to OEM specifications.
Belt Reinstallation
Properly adjusting the serpentine belt to the recommended tension is critical. Incorrect tension can lead to belt wear or alternator performance issues.
Reassembly Checklist
This checklist ensures that each reassembly step is accurately completed, guaranteeing the successful reinstallation of the alternator.
Task | Specification | Notes |
---|---|---|
Positioning | Correct alignment | Ensures efficient operation |
Bolt Tightening | OEM torque specs | Prevents over/under-tightening |
Belt Tension | Manufacturer’s spec | Ensures proper operation and longevity |
8. Final Check
Verification of Repair
A comprehensive final check is necessary to ensure the repair’s success. This includes a thorough inspection and testing of the alternator post-reinstallation to confirm everything functions as expected.
Operational Test and Voltage Recheck
Conducting an operational test and rechecking the voltage output are critical final steps. They verify that the alternator repair was successful and that the alternator operates within the required specifications.
Professional Tips
Expert Insights
For successful alternator repair, adhering to specific guidelines and using the right tools are paramount. Referring to the vehicle’s service manual for detailed instructions and using calibrated tools for measurements are essential for a reliable repair.
Expert Advice Table
This table offers quick expert advice on various aspects of alternator repair, emphasizing the importance of precision and informed decision-making.
Tip | Explanation | Benefit |
---|---|---|
Service Manuals | Provides vehicle-specific instructions | Ensures accuracy in repair |
Calibrated Tools | Essential for precise measurements | Increases reliability of repair |
Cost Analysis | Repair vs. replacement | Cost-effective decision-making |
Bolt Size | Torque Specification | Notes |
---|---|---|
M8 | 20-25 Nm | Common for smaller brackets |
M10 | 30-35 Nm | Standard for medium-sized vehicles |
M12 | 35-40 Nm | Used in larger or heavy-duty alternators |

The lambdageeks.com Core SME Team is a group of experienced subject matter experts from diverse scientific and technical fields including Physics, Chemistry, Technology,Electronics & Electrical Engineering, Automotive, Mechanical Engineering. Our team collaborates to create high-quality, well-researched articles on a wide range of science and technology topics for the lambdageeks.com website.
All Our Senior SME are having more than 7 Years of experience in the respective fields . They are either Working Industry Professionals or assocaited With different Universities. Refer Our Authors Page to get to know About our Core SMEs.